<< Back
_
Steps of a Construction Project
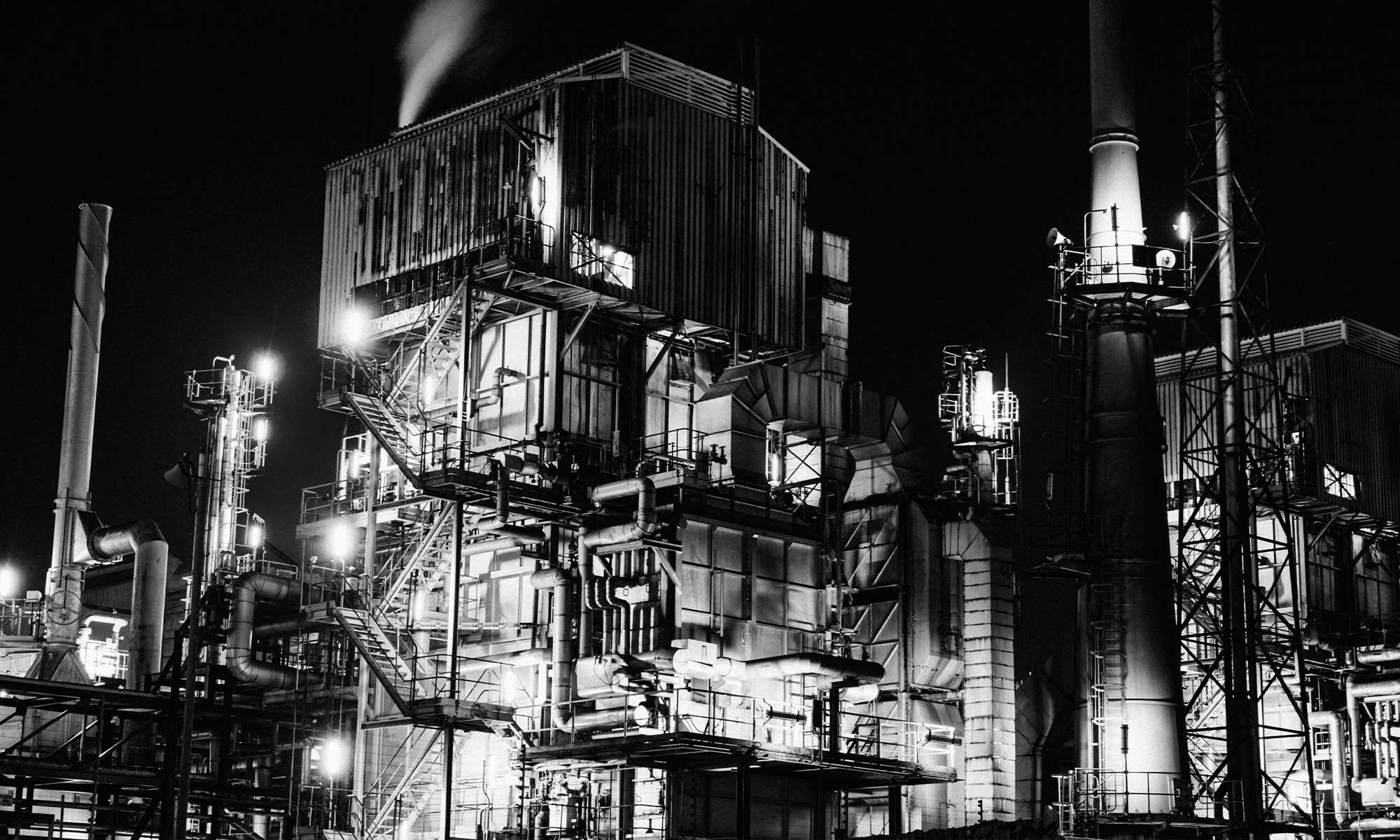
PRECONSTRUCTION
Space Assessment:
- Identify space and square footage needed.
- List equipment, their locations in the space, and cutsheets (power/utility requirements, foundation requirements, dimensions).
- Note any specialty requirements:
- Exhaust systems
- Temperature, humidity, or cleanliness controls
- Data connectivity
- Grounding
- Blast/radiation shielding
- Oxygen monitors, mist systems, or static control
Factory Planning:
- Create a detailed layout using PDF, CAD, or paper sketches.
- Consider:
- Proximity to utilities and sewers
- Allowance for future growth
- Placement of “monuments” (fixed equipment or structures)
- Equipment access (e.g., head height, door size)
- Proximity to shipping/receiving or inventory areas
Cost and Schedule Estimation:
- Use industry data, geographical data, and supply chain variables to estimate costs and timelines.
- Reference RSMeans or other reliable data sources.
- Gather rough costings from general contractors (GCs) or subcontractors and create a draft schedule.
- Internal Approvals:
- Greenlight rough costing and schedule internally.
- External Approvals:
- Obtain notional landlord approval.
- Engage with county or municipal authorities.
- Design Team:
- Hire an architect/design team or opt for a design-build firm.
- Delivery Model Considerations:
- Design-Bid-Build: Sequential process, more control over each step, but higher administrative burden and potential for cost overruns.
- Design-Build: Streamlined process, less oversight required, but less control and potential contractual risks.
APPROVALS
Internal Approvals
- Finalize the schedule with clear deadlines and contingency plans.
- Agree on budget and explore low, medium, and high-cost options.
- Make value tradeoffs if necessary, considering risks to performance, quality, and safety.
- Obtain formal project approval with contingency funds allocated.
External Approvals
- Navigate city/county permitting for:
- Building, structural, architectural, MEP (mechanical, electrical, plumbing), fire.
- Over-the-counter or deferred approvals as applicable.
- Obtain landlord approvals if required by the lease.
- Address any environmental or specialty permitting (e.g., battery storage, paint booths, waste disposal, test processes, nuclear permits).
CONSTRUCTION
Pre-Construction
- Identify long-lead items (e.g., HVAC units, electrical equipment, manufacturing equipment, cranes) and order them directly if feasible.
- Pros: Avoid contractor fees, ensure timely arrival.
- Cons: Owner assumes responsibility for receipt, coordination, and accuracy.
- Bid out plans to:
- Licensed general contractors for full management.
- Individual subcontractors if pursuing the Owner-Builder approach.
Bid Comparisons
- Level bids: Compare scope, cost, and schedule differences.
- Flag discrepancies and ask clarifying questions.
- Select contractor(s) based on alignment with project priorities.
- Sign contracts using AIA templates or other standardized agreements.
Construction Execution
- Conduct a pre-construction meeting with all stakeholders to align on goals and expectations.
- Begin work once approvals are in place.
- For any pending approvals, identify tasks that can commence to minimize delays.
- Hire a deputy inspector (required by county regulations and good practice).
- Manage day-to-day operations with the GC or subcontractors, addressing unforeseen field conditions as they arise.
- Coordinate city inspections as required.
- Keep the landlord informed per lease requirements.
Closeout
- Contractor completion and punch walk:
- Identify deficiencies (e.g., paint scuffs, missing components).
- Ensure resolution before final payment.
- Collect closeout documents:
- Warranties, O&M reports, as-built documents.
MAINTENANCE
- Transition the project to your facilities team or property manager.
- Provide all documentation and training for ongoing maintenance.
- Conduct a post-occupancy review (3-6 months after completion) to assess performance and address any issues.
Published
February 10, 2025